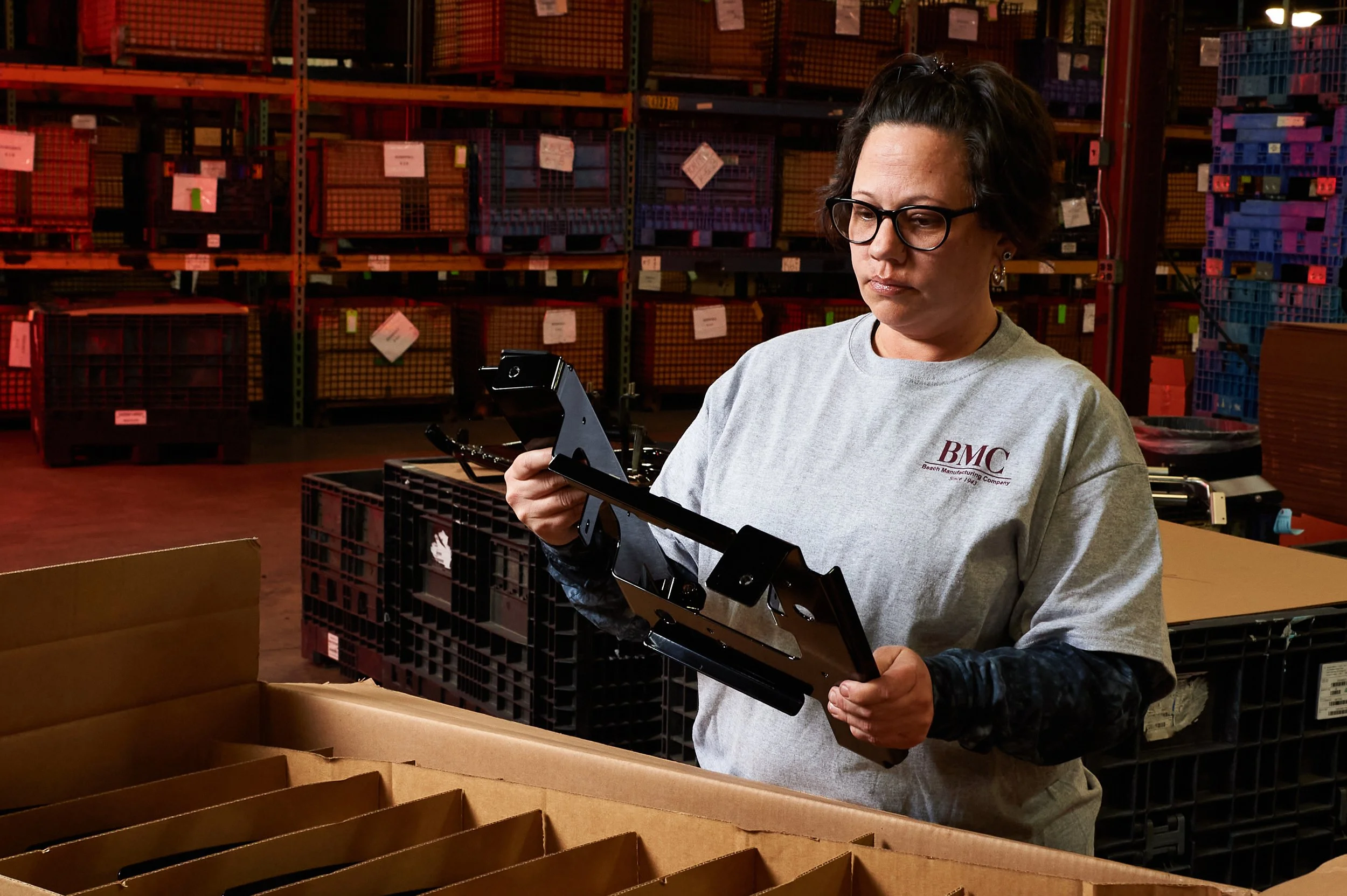
What We Do
Since 1943, we have led the effort to permanently change the trucking industry by manufacturing the first heated mirror. Today, we continue that tradition in medical, aviation and military.
Beach Manufacturing Company (BMC), Inc., has succeeded where others have failed by combining a heritage of friendly, small-town tradition with a strong work ethic and a knack for innovation. Based in Donnelsville, Ohio, the thriving 75-year-old family business operates six facilities and supplies parts to large truck, bus and military organizations, as well as the agricultural industry and other commercial and consumer markets. The company’s mission is to be a leader in development and production, to meet or exceed customer expectations, and to commit to the on-time delivery of quality products.
Beach Manufacturing Company family owned since 1943.
In addition to manufacturing expertise, BMC offers design services and counts talented engineers among its 90-member team. Jobs range from custom work to large production runs, which makes for a diverse and challenging shop floor.
BMC purchased its first laser and air-bending press brakes in 2013, when it also acquired the Radan CAD/CAM solution for sheet metal, by Vero Software, to program the new equipment. While Radan is used by BMC to program the laser, Radan Radbend is a specialized bending solution used to drive the press brakes.
MAZAK
“We have one Mazak Optiplex 3015 II laser, one Mazak Optiplex 3015 Fiber II laser and two Accurpress air-bending press brakes — all of which work fluidly with Radan and Radbend software,” Eliot Baggs says. “Within the company, we also have a variety of presses for bending, die stamping and forming. We do roboticwelding at one location, build truck mirrors at another, and paint our finished parts at yet another facility. We’re just a well-rounded truck components supplier.” Parts at BMC are made in aluminum and various steels, and jobs range from smaller, very custom projects to larger production runs. To fulfill its design needs, the company uses both SOLIDWORKS®, by Dassault Systèmes, and Solid Edge®, by Siemens PLM Software. Radan works well with both systems, says Baggs, who appreciates the flexibility of programming with the solution.
Heated Truck Mirror
BMC CAPABILITES
Laser Cutting
Beginning in 2013, BMC added laser cutting to its wide array of metal working capabilities. Initially, (1) 4kW Mazak laser was installed. Since that time we have added a 2nd 4kW laser (2014) and a 10 shelf, automated feed system (2015). BMC utilizes these lasers to cut a wide variety of materials and thicknesses of both ferrous and non-ferrous materials.
Beginning in August 2016, we announce the addition of our 1st 6kW Mazak laser. With this addition, BMC will be able to utilize the latest in laser cutting technologies.
Press Brake
Also beginning in 2013, BMC invested in state of the art Accurpress and Amada press brakes. With capacities ranging from 75 ton – 175 ton, we further expand our ability to better service our customers.
Metal Stamping and Forming
BMC's stamping capabilities range from 25 to 400 tons. Press brakes, coil feeders, and straightners, give BMC a competitive edge in stamping capability.
Tube Bending
Since 1943
BMC offers horizontal CNC tube bending, vertical tube bending, swaging, and various other end forming of tubing, pipe, and solid rod. BMC can bend 3/8 to 5 inch tubing and solid bar up to 1 inch. BMC owns an array of benders to efficiently handle all size jobs. BMC offers end forming capabilities including swaging, threading, and beading.
Welding
BMC is certified through Applications Technologies Company to weld to Government standards. BMC offers MIG and TIG welding for steel, stainless, and aluminum applications. BMC also has experience welding pressurized vessels including fuel tanks and surge tanks.
Powder coating
BMC offers durable weather resistant coatings with base coat and topcoat capabilities with one pass.
75-year-old family business operating six facilities
What We’ve Achieved
Manufactured first Heated Mirror
Hummer and military components
75 years in business
Producing over 4,000 sku numbers
Ability to program tooling at the part level
High yield of production parts using the least amount of time and material
6 facility campuses
In-house engineering team
Ability to plan jobs before they’re sent to the machine
Flexibility in lights-out production
One-stop-shop
On time delivery of quality products